Rubber molded components are manufactured by a process known as rubber molding, which involves shaping uncured rubber into a specific form or design. This process utilizes a mold, often made of metal or other materials, which is filled with the uncured rubber material. The rubber is then subjected to heat and pressure to cure and solidify, resulting in the desired shape. The mold is then opened, and the finished rubber component is removed.
Rubber O Rings
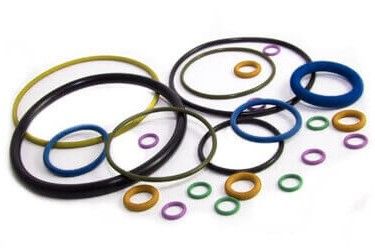
Rubber O-rings are essential sealing components used in a wide array of industries and applications. These small, circular rings play a vital role in creating reliable seals, preventing leaks, and maintaining the efficiency of various systems. In this comprehensive note, we will delve deeper into the world of rubber O-rings, exploring their structure, materials, manufacturing process, applications, and advantages.
1] Structure and Design:
Rubber O-rings are named after their distinctive shape, which resembles the letter “O” when viewed from a cross-section. They are typically made of elastomers, which are rubber-like materials with excellent flexibility and resilience. The most commonly used elastomers for O-rings include nitrile rubber (NBR), silicone rubber (VMQ), fluorocarbon rubber (FKM), and ethylene propylene diene monomer (EPDM).
Materials and Properties:
The choice of rubber material for O-rings depends on the specific requirements of the application. Different elastomers offer varying properties and characteristics:
a) Nitrile Rubber (NBR):
NBR O-rings are known for their excellent resistance to oils, fuels, hydraulic fluids, and many common solvents. They exhibit good mechanical properties, low compression set, and moderate temperature resistance (-40°C to +120°C). NBR is widely used in automotive, oil and gas, and general industrial applications.
b) Silicone Rubber (VMQ):
VMQ O-rings have outstanding high-temperature resistance (-60°C to +230°C), low toxicity, and excellent flexibility over a wide temperature range. They are commonly used in food and beverage, medical, and pharmaceutical applications.
c) Fluorocarbon Rubber (FKM):
FKM O-rings offer exceptional resistance to high temperatures (-20°C to +250°C), chemicals, fuels, and oils. They are commonly used in aerospace, automotive, and chemical processing industries.
d) Ethylene Propylene Diene Monomer (EPDM):
EPDM O-rings are known for their excellent resistance to weathering, ozone, water, and steam. They have a wide temperature range (-50°C to +150°C) and are commonly used in outdoor applications, water systems, and automotive cooling systems.
Manufacturing Process:
The production of rubber O-rings involves several key steps:
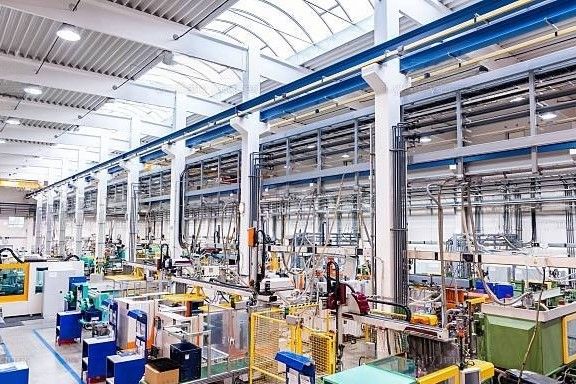
a) Material Mixing:
The chosen elastomer is mixed with various additives, including curing agents, accelerators, and fillers, to achieve the desired properties and improve processability.
b) Extrusion or Injection Molding:
The rubber compound is shaped into a continuous profile using extrusion or injection molding processes. Extrusion involves forcing the compound through a die to form a continuous cylindrical shape, which is then cut into individual O-rings. Injection molding involves injecting the compound into a mold cavity shaped like the O-ring, where it is cured and solidified.
c) Curing:
The shaped O-rings are then subjected to heat and pressure in a curing process, allowing the rubber to vulcanize and achieve its final properties. The curing process ensures the O-rings maintain their shape, elasticity, and sealing capabilities.
PRESSURE COOKER GASKETS
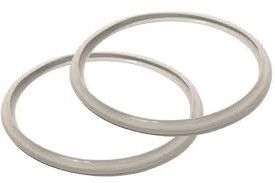
A pressure cooker gasket, also known as a sealing ring or rubber ring, is a circular band typically made from food-grade silicone or rubber. This flexible ring serves as a seal between the lid and the pot of a pressure cooker. When properly fitted, the gasket forms an airtight seal that prevents steam from escaping, creating a pressurized environment within the cooker.
The main purpose of the gasket is to maintain high internal pressure, which enables food to cook faster by raising the boiling point of water. As the temperature inside the pressure cooker increases, so does the pressure, resulting in shorter cooking times compared to conventional methods. This energy-efficient cooking technique also helps to retain the natural flavors, textures, and nutritional value of the food being prepared.
Now, let’s delve into the various aspects and functions of pressure cooker gaskets:
1] Sealing:
The gasket’s primary function is to ensure a tight seal between the lid and the pot, preventing any steam or pressure from escaping during cooking. The seal is critical for achieving the desired pressure levels required for efficient cooking.
2] Safety:
Pressure cookers are designed with built-in safety mechanisms, such as pressure release valves. However, without a properly functioning gasket, these safety features can be compromised. A faulty gasket might lead to excessive pressure buildup, potentially resulting in accidents or damage to the cooker.
3] Durability:
Pressure cooker gaskets are designed to withstand high temperatures and pressure over prolonged periods. However, they are not invincible and may wear out over time due to regular use, exposure to heat, and the natural aging process of the material. It is important to inspect and replace the gasket periodically to ensure optimal performance and safety.
4] Maintenance:
Proper maintenance of the gasket is essential to ensure its longevity. Regular cleaning and inspection can help prevent the accumulation of food particles, oil residues, and debris, which could affect the gasket’s ability to form a tight seal. Follow the manufacturer’s guidelines for cleaning and storing the gasket, as some may be dishwasher safe while others require hand washing.
5] Replacement:
As mentioned earlier, gaskets will eventually wear out and lose their elasticity, compromising their sealing capabilities. It is recommended to replace the gasket every 12 to 18 months or as advised by the manufacturer. A damaged or worn-out gasket should be promptly replaced to maintain the cooker’s performance and safety standards.
In conclusion, pressure cooker gaskets play a vital role in maintaining the integrity and efficiency of pressure cooking. By creating an airtight seal, they allow for the generation and retention of high pressure, resulting in faster cooking times and better culinary outcomes. Regular inspection, cleaning, and timely replacement of gaskets are crucial for optimal performance and safety.
I hope this information proves useful to you in understanding the importance of pressure cooker gaskets. Should you have any further queries or require additional assistance, please do not hesitate to reach out.
Rubber Square Rings
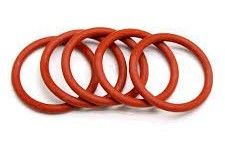
I hope this note finds you well. Today, I would like to shed some light on the topic of rubber square rings and their wide-ranging applications across various industries. Rubber square rings, also known as square-section seals or square-profile seals, are versatile components that offer reliable sealing solutions in diverse mechanical and engineering systems. Let’s delve into the features, functions, and applications of these remarkable seals.
Design and Construction:
Rubber square rings are typically made from high-quality elastomers, such as natural rubber, synthetic rubber (e.g., neoprene, nitrile, silicone), or fluoroelastomers (e.g., Viton®). These materials provide excellent resistance to heat, chemicals, weathering, and mechanical stress. The square shape of the ring allows for uniform compression and reliable sealing in both static and dynamic applications.
Sealing Function:
The primary purpose of rubber square rings is to provide an effective seal between two mating surfaces. They are designed to prevent the leakage of fluids (liquids or gases) and the ingress of contaminants (e.g., dust, dirt, moisture) into a system. The square cross-section of these rings ensures even distribution of sealing force, resulting in enhanced sealing performance and durability.
Applications:
Rubber square rings find application in a wide range of industries and sectors. Some notable examples include:
a. Automotive Industry:
Square rings are utilized in various automotive components, such as engines, transmissions, hydraulic systems, brake systems, and fuel systems. They provide sealing solutions for cylinders, pistons, pumps, valves, and other critical components.
b. Industrial Machinery:
Square rings are employed in machinery and equipment for sealing hydraulic and pneumatic systems, including cylinders, actuators, valves, and pumps. They ensure leak-free operation and help maintain system efficiency.
c. Aerospace and Defense:
In the aerospace and defense sectors, rubber square rings are used in aircraft engines, landing gear systems, hydraulic systems, and missile systems. They provide dependable sealing in demanding environments and under extreme operating conditions.
d. Manufacturing and Processing:
Rubber square rings are utilized in manufacturing and processing industries for sealing fluid and gas lines, connectors, and fittings. They help maintain the integrity of systems and prevent costly leaks and downtime.
e. Plumbing and HVAC:
Square rings are employed in plumbing systems, faucets, valves, and HVAC (heating, ventilation, and air conditioning) equipment. They ensure watertight seals and prevent leakage in residential, commercial, and industrial applications.
In conclusion, rubber square rings are indispensable sealing components that find applications across diverse industries and sectors. Their ability to provide reliable sealing, resist various environmental factors, and accommodate dynamic and static applications makes them a popular choice for engineers and designers. Whether in automotive systems, industrial machinery, aerospace, or plumbing applications, rubber square rings offer dependable sealing solutions for enhanced performance, safety, and efficiency.
I hope this information provides you with valuable insights into the significance and versatility of rubber square rings.
Oil Seals
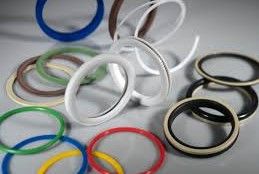
Understanding the Importance and Functionality of Oil Seals
I hope this note finds you well. Today, I would like to delve into the topic of oil seals, also known as shaft seals or rotary seals, and discuss their significance, functions, and applications across various industries. Oil seals are essential components designed to prevent the leakage of fluids, primarily lubricating oil, from rotating or reciprocating shafts in machinery and equipment. Let’s explore the fascinating world of oil seals together.
Design and Construction:
Oil seals are typically composed of three main components:
Outer Metal Case: This component provides structural support and helps secure the seal in its housing.
Elastomer or Rubber Material: The primary sealing element is made of high-quality elastomers, such as nitrile rubber (NBR), fluoroelastomers (e.g., Viton®), or silicone rubber. These materials offer excellent resistance to heat, chemicals, wear, and compression set.
Spring: Many oil seals feature an internal spring, which ensures consistent contact between the sealing lip and the rotating shaft. This spring helps maintain the seal’s effectiveness even in the presence of shaft misalignment or variations in speed.
Sealing Function:
The primary function of an oil seal is to prevent the leakage of oil or other lubricants from the machine’s housing, particularly where a rotating or reciprocating shaft passes through a stationary housing or bearing. The seal creates a physical barrier, providing a tight and reliable seal between the shaft and the housing, thus maintaining lubrication and preventing contamination or loss of fluids.
Applications:
Oil seals are widely used in various industries and applications, including:
Automotive Industry: Oil seals are found in engines, transmissions, differential units, axles, and wheel hubs of vehicles. They prevent oil leakage and help maintain optimal lubrication for smooth and efficient operation.
Industrial Machinery: Oil seals are crucial components in industrial machinery, such as pumps, compressors, gearboxes, motors, and hydraulic systems. They provide sealing solutions for shafts, bearings, and other critical rotating or reciprocating parts.
Power Generation: Oil seals are utilized in power generation equipment, including turbines, generators, and wind turbines. They help maintain proper lubrication and prevent oil leakage, ensuring reliable operation and extending the lifespan of the equipment.
Aerospace and Defense: Oil seals find applications in aerospace and defense systems, including aircraft engines, landing gear, hydraulic systems, and missile systems. They ensure efficient lubrication and prevent the ingress of contaminants, contributing to the safety and reliability of these systems.
Marine and Offshore: In marine and offshore environments, oil seals are employed in ship propulsion systems, propeller shafts, thrusters, and various equipment. They protect against water ingress and maintain effective lubrication in harsh conditions
Advantages:
- Oil seals offer several advantages, including:
- Leakage Prevention: Oil seals effectively prevent the leakage of lubricating oil or other fluids, reducing the risk of equipment damage and ensuring continuous operation.
- Contamination Protection: These seals act as a barrier, preventing contaminants like dust, dirt, water, and debris from entering the system, thereby safeguarding the equipment and maintaining its performance.
- Lubrication Retention: By preventing oil leakage, oil seals help ensure that the critical components of machinery and equipment receive adequate lubrication, reducing friction and wear.
- Versatility: Oil seals are available in various sizes, materials, and designs to accommodate different applications, operating conditions, and temperature ranges.
In conclusion, oil seals play a vital role in maintaining the integrity, performance, and longevity of machinery and equipment across multiple industries.
Gas Washers
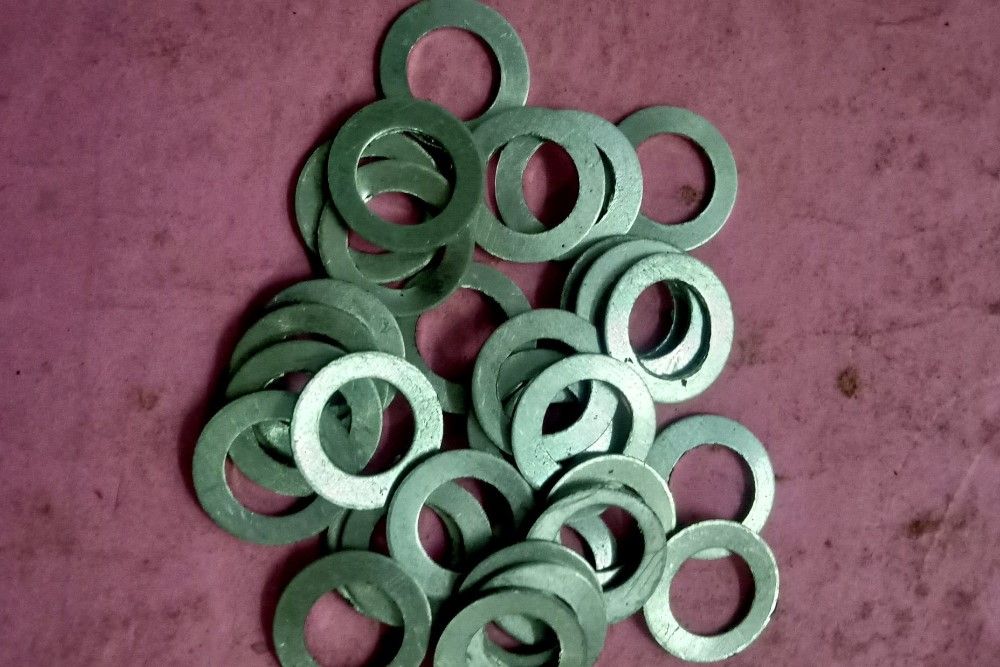
Enhancing Efficiency and Safety in Gas Systems:
hope this note finds you well. Today, I would like to discuss the importance and functionality of gas washers, also known as gas seals or gas-tight washers. Gas washers are integral components used in gas systems to provide a reliable and secure sealing solution between threaded connections. They play a crucial role in enhancing efficiency, preventing gas leaks, and ensuring the safety of gas-related operations. Let’s delve into the fascinating world of gas washers together.
Design and Construction
Gas washers are typically made from durable and chemically resistant materials such as rubber, silicone, or fiber-reinforced composites. They are designed to fit between two mating surfaces, typically threaded connections, creating a gas-tight seal. Gas washers come in various sizes and shapes, including flat washers, O-ring washers, and gasket washers, to accommodate different connection types and applications.
Sealing Function
The primary function of gas washers is to create a reliable and leak-proof seal between threaded connections in gas systems. When properly installed, gas washers compress between the mating surfaces, exerting pressure on the threads and forming an airtight seal. This sealing action prevents the escape of gas, ensuring the integrity and efficiency of the gas system.
Applications
Gas washers find applications in a wide range of industries and sectors where gas systems are employed. Some notable examples include:
a. Gas Appliances: Gas washers are used in various gas-powered appliances such as stoves, ovens, water heaters, and furnaces. They ensure a secure seal between the gas supply line and the appliance, preventing gas leaks and promoting efficient operation.
b. Industrial and Commercial Gas Systems: Gas washers are vital components in industrial and commercial settings where gas systems are utilized. They are commonly found in pipelines, valves, regulators, meters, and other gas-handling equipment. The washers help maintain gas tightness and prevent leakage in critical applications.
c. Automotive and Transportation: Gas washers are utilized in automotive and transportation sectors, particularly in fuel systems. They provide a reliable seal between components such as fuel lines, fuel injectors, and carburetors, ensuring proper fuel delivery and preventing gas leaks.
d. Energy and Utilities: Gas washers play a crucial role in energy and utility sectors where gas systems are integral to operations. They are used in gas pipelines, distribution systems, meters, and pressure regulators, ensuring the safe and efficient supply of gas.
Conclusion
Gas washers provide a powerful cleaning solution with their high-pressure water streams and robust gasoline engines. Their portability, versatility, and superior cleaning capabilities make them highly sought after
Rubber Bushes
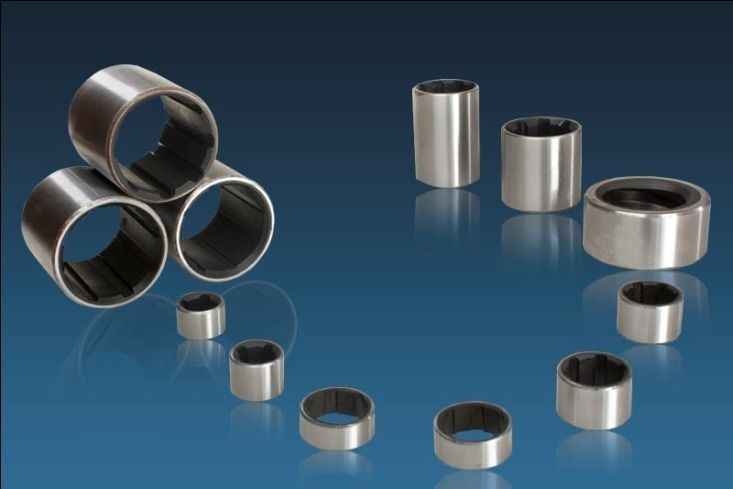
An Essential Component for Smooth and Reliable Machinery Operation
Rubber bushes are a crucial component in various mechanical systems, providing crucial support and damping capabilities. These small but essential components play a significant role in reducing noise, vibration, and harshness (NVH) levels, ensuring smooth and reliable machinery operation. Rubber bushes are widely used in industries such as automotive, aerospace, construction, and machinery manufacturing. This note will delve into the characteristics, applications, benefits, and maintenance considerations of rubber bushes, highlighting their importance in modern engineering.
Characteristics of Rubber Bushes:
Rubber bushes are made from a combination of rubber compounds and metal inserts. The rubber used in their construction is typically a specialized elastomer, chosen for its excellent resilience, durability, and resistance to environmental factors such as heat, oil, and chemicals. The metal inserts, often made of steel, provide structural support and ensure proper alignment within the machinery.
Applications of Rubber Bushes:
- Automotive Industry: Rubber bushes find extensive use in the automotive industry, where they are employed in suspension systems, engine mounts, stabilizer bars, and various chassis components. They absorb shocks and vibrations, ensuring a smoother and more comfortable ride for the vehicle occupants.
- Aerospace Industry: In the aerospace sector, rubber bushes are utilized in landing gear systems, engine mounts, and other critical areas. Their ability to absorb vibration and dampen noise is crucial for enhancing passenger comfort and minimizing component wear and fatigue.
- Machinery Manufacturing: Rubber bushes are employed in various machinery applications, including pumps, compressors, generators, and industrial equipment. They minimize the transmission of vibrations and noise, protecting both the machinery and the surrounding environment.
Benefits of Rubber Bushes:
- Vibration Damping: Rubber bushes act as excellent isolators, absorbing vibrations generated by machinery and preventing their propagation to other components. By minimizing vibrations, rubber bushes contribute to improved machinery performance, reduced component wear, and increased service life.
- Noise Reduction: The elasticity and resilience of rubber bushes help in dampening noise generated by mechanical systems. By absorbing and dissipating the vibrations that cause noise, rubber bushes significantly reduce overall noise levels, creating a quieter operating environment.
- Improved Stability and Comfort: In automotive applications, rubber bushes play a crucial role in enhancing stability, handling, and ride comfort. They provide necessary flexibility, allowing controlled movement while maintaining structural integrity.
- Alignment and Positioning: Rubber bushes ensure accurate alignment and positioning of various components within machinery. They help maintain proper clearances, reduce friction, and prevent metal-to-metal contact, thus preventing premature wear and damage.
Plastic Parts
I hope this note finds you well. Today, I would like to discuss a topic that has become increasingly relevant in our modern world: plastic parts. Plastic parts have revolutionized various industries and are prevalent in countless aspects of our daily lives. From the tiniest electronic components to large-scale machinery, plastic parts play a vital role in shaping our modern society.
Plastic parts are manufactured using a process called injection molding, which involves injecting molten plastic into a mold cavity. This method allows for the production of complex and intricate shapes, making plastic parts versatile and adaptable to a wide range of applications. The ability to mold plastic into virtually any form has made it a preferred material choice for manufacturers across industries.
One of the key advantages of plastic parts is their cost-effectiveness. Plastic materials are generally more affordable compared to other alternatives such as metal or glass. This affordability makes plastic parts an attractive option for mass production, allowing companies to produce large quantities at a lower cost per unit. As a result, consumer goods like toys, packaging materials, and household appliances can be manufactured more affordably, making them accessible to a broader range of consumers.
In addition to being cost-effective, plastic parts offer numerous other benefits. Firstly, they are lightweight, which makes them ideal for applications where weight reduction is crucial, such as in the automotive and aerospace industries. The use of plastic parts in these sectors helps to improve fuel efficiency and reduce emissions, contributing to a more sustainable future.
Furthermore, plastic parts possess excellent strength-to-weight ratios, meaning they can be strong and durable while maintaining a low weight. This characteristic is especially advantageous in industries like construction and manufacturing, where components need to withstand heavy loads and repetitive stress. Plastic parts are also resistant to corrosion, moisture, and chemicals, ensuring their longevity in various environments.
The versatility of plastic parts extends beyond their physical properties. Plastic materials can be formulated to possess specific characteristics, such as flexibility, transparency, or heat resistance, depending on the intended application. This ability to tailor the material’s properties allows for customized solutions in diverse industries, ranging from medical devices to consumer electronics.
However, it is essential to acknowledge the environmental concerns associated with plastic parts. Plastics, especially those that are non-biodegradable, can have detrimental effects on ecosystems if not managed properly. The improper disposal and excessive use of single-use plastics have contributed to the pollution of our oceans and landfills. As responsible consumers, it is our duty to minimize plastic waste by recycling and supporting sustainable alternatives whenever possible.
Efforts are being made to address these concerns and promote the use of eco-friendly materials and practices in the production of plastic parts. For instance, there is a growing trend towards using biodegradable or compostable plastics derived from renewable sources, such as plant-based materials. Additionally, recycling programs and initiatives are being implemented globally to reduce plastic waste and promote a circular economy.
In conclusion, plastic parts have become an integral part of our modern world, offering a wide range of benefits across various industries. Their affordability, versatility, and durability have made them indispensable in countless applications, from everyday consumer goods to complex industrial machinery. However, it is crucial that we remain mindful of the environmental impact of plastic waste and work towards sustainable solutions.
Let us strive to make responsible choices in our consumption, support initiatives that promote recycling and the use of eco-friendly materials, and encourage innovation in the development of sustainable alternatives. Together, we can create a future where plastic parts continue to play a significant role while minimizing their impact on the environment.
Thank you for taking the time to read this note. If you have any further questions or would like to discuss this topic in more detail, please do not hesitate to reach out.
Solar Rubber Parts
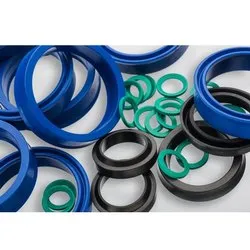
Exploring the Benefits of Solar Rubber Parts
In today’s rapidly evolving world, the need for sustainable and renewable energy sources has become increasingly apparent. Solar power, in particular, has emerged as a promising solution to meet our energy demands while reducing our carbon footprint. As the solar industry continues to expand, innovative technologies and components are being developed to enhance the efficiency and durability of solar systems. One such advancement is the use of solar rubber parts, which offer numerous benefits in harnessing the power of the sun. In this article, we will delve into the world of solar rubber parts, exploring their advantages and applications.
Understanding Solar Rubber Parts
Solar rubber parts are specialized components designed specifically for solar power systems. These parts are manufactured using high-quality rubber materials that possess excellent weather resistance, durability, and electrical insulation properties. They are engineered to withstand the harsh environmental conditions experienced in solar installations, including exposure to sunlight, extreme temperatures, moisture, and physical stress.
Advantages of Solar Rubber Parts
- Enhanced Weather Resistance: Solar rubber parts are formulated to withstand prolonged exposure to UV radiation and extreme weather conditions. They offer excellent resistance to degradation caused by sunlight, ensuring their longevity and reliability in outdoor environments.
- Improved Sealing and Protection: Solar rubber parts act as effective seals, preventing the ingress of dust, water, and other contaminants into the solar system components. This helps to maintain the integrity of the system and protects delicate electronics, such as solar panels, junction boxes, and connectors.
- Vibration and Shock Absorption: Solar installations are subject to various types of vibrations and shocks, such as those caused by wind, transportation, and equipment operations. Rubber parts, with their inherent elasticity and damping properties, provide effective vibration and shock absorption, reducing the risk of damage and enhancing the overall system performance.
- Electrical Insulation: Rubber materials used in solar parts possess excellent electrical insulation properties. This ensures that the components can safely isolate and protect electrical connections, preventing potential electrical hazards and ensuring the system’s efficient operation.
- Versatile Applications: Solar rubber parts find application in various components of a solar system, including mounting systems, panel frames, cable management systems, junction boxes, connectors, and gaskets. Their versatility allows for seamless integration and compatibility with different solar system configurations.
Conclusion
Solar rubber parts play a vital role in enhancing the efficiency, durability, and performance of solar power systems. With their exceptional weather resistance, sealing capabilities, vibration absorption, electrical insulation, and versatility, these components contribute to the overall reliability and longevity of solar installations. As the demand for renewable energy continues to rise, the importance of reliable solar components becomes paramount. Solar rubber parts are a testament to the ongoing innovation and development within the solar industry, ensuring that we can harness the power of the sun effectively while reducing our impact on the environment.
By adopting and implementing solar rubber parts, we take a step closer to achieving a sustainable and clean energy future, where solar power becomes an integral part of our global energy mix.
Exploring Automotive Filter Rubber Parts
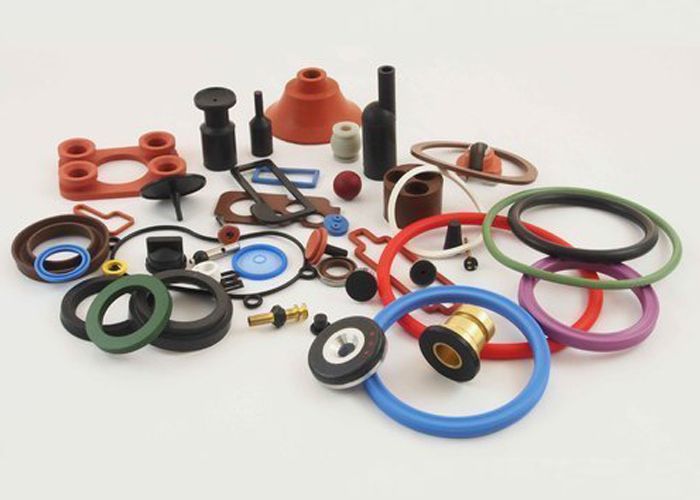
When it comes to the smooth functioning and longevity of an automobile, various components work in harmony to ensure optimal performance. One crucial aspect often overlooked is the role of automotive filter rubber parts. These seemingly small components play a significant role in maintaining the efficiency and reliability of a vehicle’s filtration system. In this article, we will delve into the importance of automotive filter rubber parts and highlight their contributions to the overall performance and durability of vehicles.
The Role of Automotive Filter Rubber Parts:
- Automotive filter rubber parts, including gaskets, seals, and o-rings, are integral to the proper functioning of a vehicle’s filtration system. They act as a barrier between different components, preventing leaks, maintaining pressure, and ensuring a secure fit. The primary purpose of these parts is to create a tight seal and prevent contaminants from entering critical systems, such as the engine, fuel, or air intake.
- Maintaining Optimal Performance: Efficient filtration is crucial for maintaining the performance and longevity of a vehicle’s engine. Automotive filter rubber parts help ensure that contaminants, such as dirt, dust, debris, and even moisture, are effectively captured and prevented from entering sensitive areas. By preventing these harmful particles from reaching the engine, the rubber parts help reduce the risk of engine wear, corrosion, and potential damage, thereby optimizing performance.
- Enhancing Durability: In addition to their role in maintaining performance, automotive filter rubber parts contribute significantly to the durability of various components. By creating a secure seal, they help protect sensitive systems from the ingress of foreign materials that could cause premature wear or damage. Moreover, these rubber parts exhibit excellent resistance to temperature fluctuations, oil, chemicals, and other environmental factors, ensuring their longevity and reliability over time.
- Reducing Maintenance Costs: The installation of high-quality automotive filter rubber parts can help reduce overall maintenance costs for vehicle owners. By effectively sealing filtration systems, these parts prevent the need for costly repairs or premature replacement of critical components. Moreover, their durability and resistance to wear ensure extended service life, leading to fewer replacements and decreased downtime for repairs.
- Importance of Quality and Compatibility: To reap the full benefits of automotive filter rubber parts, it is crucial to prioritize quality and compatibility. Opt for parts that are manufactured using premium materials, such as synthetic rubbers, which offer exceptional resistance to temperature, chemicals, and aging. Additionally, ensuring compatibility with the specific make and model of the vehicle is vital to guarantee an accurate fit and optimal performance.
- Regular Inspection and Replacement: Like any other component in a vehicle, automotive filter rubber parts require regular inspection and maintenance. Over time, these parts may degrade due to exposure to environmental factors and the stresses of engine operation. Timely inspection and replacement of worn or damaged rubber parts will help maintain the integrity of the filtration system and ensure continued performance and longevity.
- Conclusion:
- Automotive filter rubber parts may be small in size, but their significance cannot be understated. From creating tight seals to preventing the ingress of contaminants, these parts play a vital role in optimizing performance and enhancing the durability of an automobile’s filtration system. By investing in high-quality rubber parts and prioritizing regular maintenance, vehicle owners can ensure the longevity and efficiency of their vehicles, reducing costs and enjoying a smoother driving experience in the long run.
Customized Rubber Molded Parts
In the world of manufacturing and engineering, customizability and precision are key factors for success. When it comes to rubber parts, customized solutions offer immense value in meeting specific design requirements and enhancing performance. In this article, we will explore the advantages and applications of customized rubber molded parts and shed light on their ability to provide tailored solutions for a wide range of industries.
- Meeting Unique Design Requirements: One of the primary benefits of customized rubber molded parts is their ability to meet unique design requirements. Unlike off-the-shelf components, these parts are specifically engineered to fit the precise specifications of a particular application. By collaborating closely with manufacturers and engineers, customized rubber parts can be designed to accommodate intricate shapes, sizes, and configurations, ensuring a perfect fit and optimal functionality.
- Precision and Consistency: Customized rubber molded parts are produced using advanced manufacturing techniques that offer exceptional precision and consistency. The use of specialized molds and equipment allows for tight tolerances and exact replication of complex geometries. This precision ensures a consistent and reliable performance of the parts, leading to enhanced overall efficiency and functionality in the intended application.
- Versatile Applications: The versatility of customized rubber molded parts is another significant advantage. These parts find applications in a wide range of industries, including automotive, aerospace, electronics, medical, and many others. From gaskets and seals to vibration dampers and O-rings, customized rubber parts can be tailored to meet the unique demands of each industry, providing reliable solutions for specific applications.
- Enhanced Performance and Durability: Customized rubber molded parts offer improved performance and durability compared to generic components. The ability to fine-tune the material properties, such as hardness, elasticity, and chemical resistance, allows manufacturers to create parts that are perfectly suited to withstand specific operating conditions. This results in enhanced resistance to wear, chemicals, temperature extremes, and other environmental factors, thereby extending the lifespan and reliability of the parts.
- Cost-Effectiveness: Contrary to popular belief, customized rubber molded parts can also be cost-effective in the long run. While the upfront costs may be higher compared to off-the-shelf options, the tailored design ensures that the parts precisely meet the requirements, eliminating the need for modifications or additional components. Moreover, the enhanced durability and performance of customized parts reduce the risk of premature failures, leading to lower maintenance and replacement costs over time.
- Collaboration with Manufacturers: Collaboration with experienced manufacturers is key when it comes to creating customized rubber molded parts. Working closely with a trusted partner who possesses extensive knowledge of rubber materials and manufacturing processes is crucial. Their expertise can help in selecting the most suitable materials, designing efficient molds, and ensuring quality control throughout the production process.
Conclusion: Customized rubber molded parts offer a myriad of advantages in terms of precision, performance, and versatility. From meeting unique design requirements to enhancing durability and reliability, these tailor-made components play a vital role in numerous industries. By collaborating with reputable manufacturers, businesses can harness the benefits of customized rubber parts and optimize their applications, leading to improved efficiency, cost-effectiveness, and customer satisfaction.